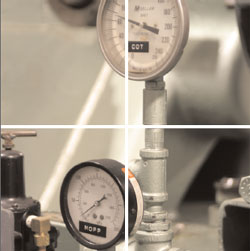 Air Energy AuditsIndependent Air Energy Audit
If you can not measure it, you cannot improve it, Lord Kelvin 1883. We therefore commence the process with a detailed survey of the compressed air system with specific focus on increasing the efficiency of compressed air usage. We start at point of use and work out way back wards to the compressor house. Always bearing in mind that if there is a less expensive compressed air alternative for a particular process, why not consider it?
Traditionally most companies measure the power consumed by the air compressor motors and relate this to the capacity of the air compressor as stated on the data plate. However, this would assume that the performance of the compressor to be the same as the day it was installed when actually it could easily be 10% or 15% down on performance.
Measuring the power provides a guide however for accurate results it is necessary to measure flow, pressure & temperature at the point where the air feeds into the distribution system.
Our experience enables us to provide the necessary justification for SMEs to obtain interest free Carbon Trust Loans, providing that they meet the necessary qualification criteria. The loan repayments would be funded by the energy savings made following the installation of an energy saving package. So, upgrading your factory could cost nothing!
|
Energy Saving TheoryEnergy Saving Theory So, you want to reduce your compressed air costs and you're thinking of buying a new air compressor
are you raving Bananas!! According to Government figures the cost of ownership over a 10 year period is 30% capital purchase & servicing and 70% energy costs. Installing another air compressor is the last thing you should do!
Approximately 10% of all industrial electrical consumption in the UK is used for compressed air generation. This generally represents the largest single electrical demand for most companies. It is estimated that 25% of this electrical usage is wasted due to leakage and incorrect pressure control and 50% site wastage is common.
So, if I understand you correctly, you're planning to install a more energy efficient air compressor and then blow a significant part of its output to atmosphere! Are you sure you want to do this? You're probably going to waste 25kw for every 100kw you install. That's about £22,000 per annum at 8000 hrs at £0.1 ppkwh.
Why not reduce the air demand on the main air generation compressors and switch the ones you've have off! Now, that's different! That means less compressor servicing costs and comparatively no electrical consumption.
Using an Industrial Engineering approach, our aim is to "Switch off" main air compressor drive motors by providing products and services which reduce the air demand on the compressed air system while maintaining production requirements.
The key elements to consider are the way that the compressed air is used, leakage reduction and effective pressure control. Our Independent Air Energy Audit would quantify the energy wastage and recommend a solution to fix the problem. The last component to consider within the air system should be the compressed air generation equipment. (DETR Good Practice Guides, Energy Efficiency Best Practice Programmes)
|
Airtec Filtration & AirHire.co.uk Oil Free & Oil Flooded Compressor Spares